smartlogistix Profile
CCS Logistics have worked with SMARTLOGISTIX LTD over several years to develop and refine a software platform addressing both logistics and field engineering requirements of client organisations. The platform operates as a Cloud Service and provides real-time tracking, management and reporting of clients’ assets and engineering jobs and resources.
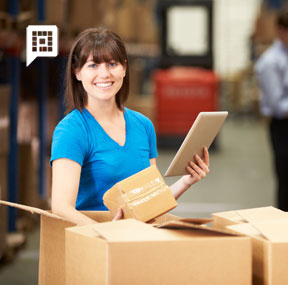
Reporting and Insight
Because every touch of an item is recorded, a complete history of its whereabouts and status is collected over time. A chain of custody of all client assets becomes available.
Everything is recorded in real-time and thus all reports reflect the current operational status of both assets and jobs. Audits may, therefore, be made at any time, at any location without the need for preparation.
CCS can provide clients with direct access to their own data via a secure website. Interfaces to clients IT systems can be made available for real-time data exchange.
Grouping and filtering of data become a powerful analysis tool providing management information and insight into client product estate and service activity.
Job counts, site history of service requests, time on site, actual versus requested actions, number of no fault found calls, can pinpoint product miss use and/or where customer training may be required.
Product MTBF and repair loop history allows clients to assess the health of their estate and make informed decisions regarding economic stock levels, inspection and triage effectiveness, disposals and introduction of new stock.
Stock and Logistics
Create products, both serialised and consumable. Where serial numbered, up to 3 identifiers can be used (e.g. serial number, MAC address, client asset number) and if the serial number pattern is known this is used to prevent miss scans and errors in data recording.
Create warehouses and bins and restrict what product types can be placed in them. Create customer projects and define which products can be used on them thus eliminating possible misuse of customer/project specific assets.
When an item is first receipted into the platform, it is assigned a unique ID, and this is used to track its status and movement history over time. This initial receipt may be new stock provided and scanned into a warehouse or faulty/return items from site received by engineer or courier.
Dispatch good stock from warehouse to engineer, courier, direct to site or another warehouse. Appropriate exchange references are recorded. Dispatches become ‘expected’ at the target location until receipted there. This allows speedy identification and resolution of missing items.
Dispatch recovered, faulty or DOA items for refurbishment or disposal. Proof of delivery is recorded. Items sent for refurbishment continue to be tracked and are ‘expected’ back within SLA. Late or missing items are easily identified, and appropriate action is taken. SLA compliance is measured.
Configuration, staging, repair and triage within a warehouse are all supported processes and recorded as part of item history.
Receive ‘expected’ items returned from engineer or courier. Sophisticated matching algorithms are used to correct any miss recorded returns (e.g. bad serial, wrong item type). The correct item is always the actual physical item after inspection and corrections are back-updated in the item history.
Engineer Activity
Create engineers for a stock location. Monitor good receipts from a warehouse or another engineer, and recoveries, faulty items and DOAs in their possession. Ensure recovered, faulty and DOA items are returned to the warehouse in a timely fashion.
Engineers receipt good stock from the warehouse (or another engineer) and can only use receipted items allowed for use on the job project for job closure. Items can also be collected from and returned to client owned or approved locations (e.g. PUDO or depot).
Create engineer jobs or import from clients. Information is provided about site location, task details including specific actions and on-site product serials, and free-form notes. Job types include install, recovery, swap-out, break-fix and service only.
Schedule engineer activity, assign or re-assign jobs depending on operational needs, resource availability and SLA proximity. Schedulers can allocate directly from Google Maps showing locations of both sites and engineers. Engineer current map location and workload is continuously updated so schedulers can maximise resource utilisation and minimise travel time.
Engineers use a mobile device and the workflow is designed and optimised for touch-driven use with the minimum of typing. Every action they take (e.g. install, recover etc.) and for every product, item is individually recorded. Signatures can be recorded as proof of job completion as well as photos of the site or equipment to support engineer actions taken.